Understanding grease technical data
Some basic knowledge is required to understand the technical data so that you can select the proper grease. This is an excerpt of the main terms mentioned in SKF grease technical data.
Consistency
A measure of the stiffness of a grease. A proper consistency will make the grease stay in the bearing without generating too much friction. It is classified according to a scale developed by the NLGI (National Lubricating Grease Institute). The softer the grease, the lower the number. Grease for bearings are typically NLGI 1, 2 or 3. The test measures how deep a cone falls into a grease sample in tenths of mm.
Classification of greases by NLGI consistency number |
NLGI
number |
ASTM worked
penetration
(10–1 mm) |
Appearance
at room
temperature |
000 |
445–475 |
very fluid |
00 |
400–430 |
fluid |
0 |
355–385 |
semi-fluid |
1 |
310–340 |
very soft |
2 |
265–295 |
soft |
3 |
220–250 |
medium hard |
4 |
175–205 |
hard |
5 |
130–160 |
very hard |
6 |
85–115 |
extremely hard |
Temperature range
Comprehends the suitable working range of the grease. It goes between the low temperature limit (LTL) and the high temperature performance limit (HTPL). LTL is defined as the lowest temperature at which the grease will allow the bearing to be started up without difficulty. Below this limit, starvation will occur and cause a failure. Above HTPL, the grease will degrade in an uncontrolled way so that grease life cannot be determined accurately.
Dropping point
Temperature at which a grease sample, when heated, will begin to flow through an opening according to DIN ISO 2176. It is important to understand that this point is considered to have limited significance for performance of the grease as it is always far above HTPL.
Viscosity
A measure of a fluid’s resistance to flow. For lubricants, a proper viscosity must guarantee an adequate separation between surfaces without causing too much friction. According to ISO standards, it is measured at 40 °C (105 °F), as viscosity changes with temperature. Values at 100 °C (210 °F) allow calculation of the viscosity index, e.g. how much the viscosity will decrease when temperature rises.
Mechanical stability
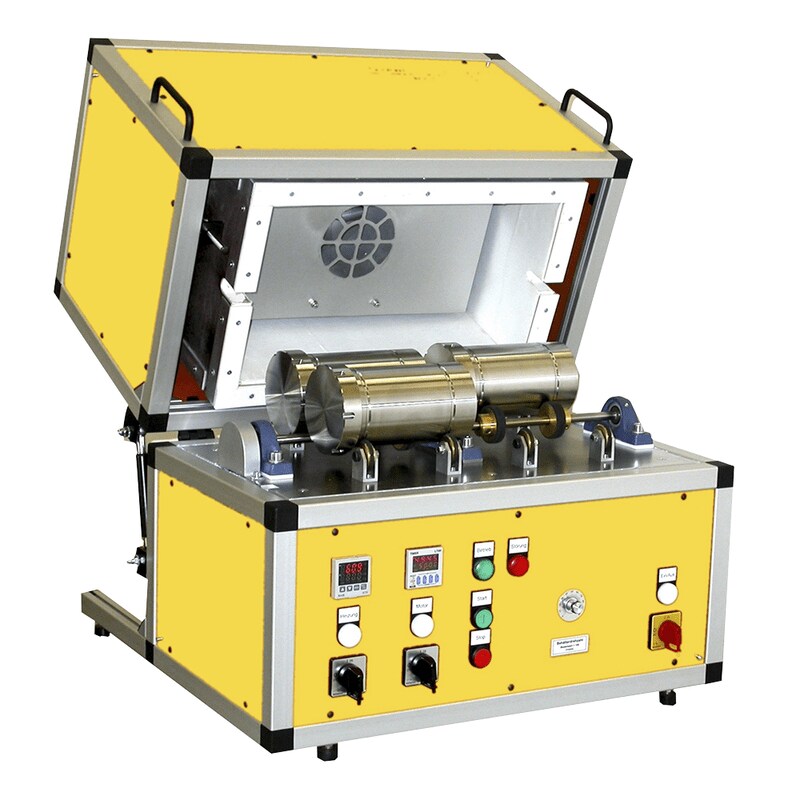
Roll stability test rig
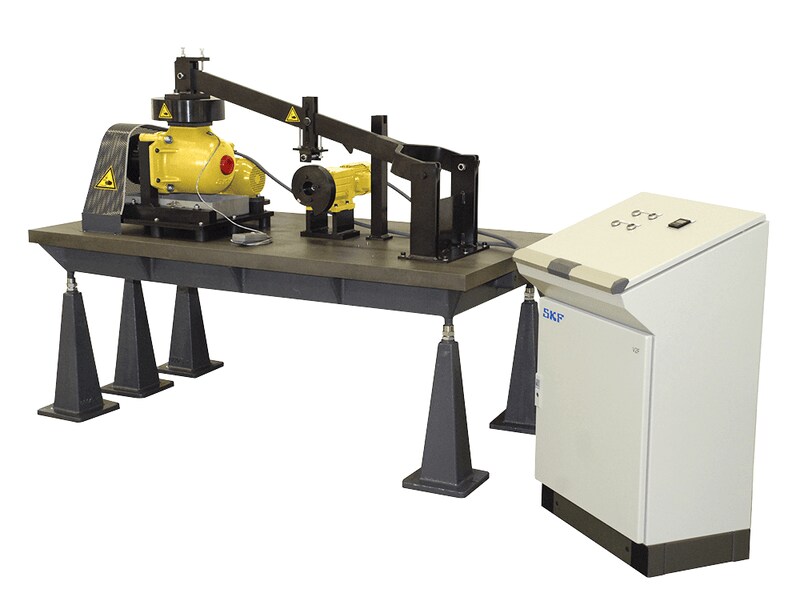
V2F grease test rig
The consistency of bearing greases should not significantly change during its working life. Three main tests are normally used to analyse this behaviour:
Prolonged penetration
The grease sample is subjected to 100 000 strokes in a device called a grease worker. Then, the penetration is measured. The difference against penetration at 60 strokes is reported as the change in 10–1 mm.
Roll stability
A grease sample is placed in a cylinder with a roller inside. The cylinder is then rotated for 72 or 100 hours at 80 or 100 °C (175 or 210 °F) (the standard test demands just 2 hours at room temperature). At the end of the test period, once the cylinder has cooled to room temperature, the penetration of the grease is measured and the change in consistency is reported in 10–1 mm.
V2F test
A railway axlebox is subjected to vibration shocks of 1 Hz from a bouncing hammer producing an acceleration level between 12–15 g. After 72 hours at 500 r/min., the grease leaked from the housing through the labyrinth seal is collected in a tray. If it weighs less than 50 g, a rating of ‘m’ is granted, otherwise it is rated as ‘fail’. Afterwards, the test is continued for another 72 hours at 1 000 r/min. If less than 150 grams of grease leaked after completion of both tests, then a rating of ‘M’ is given.
Corrosion protection
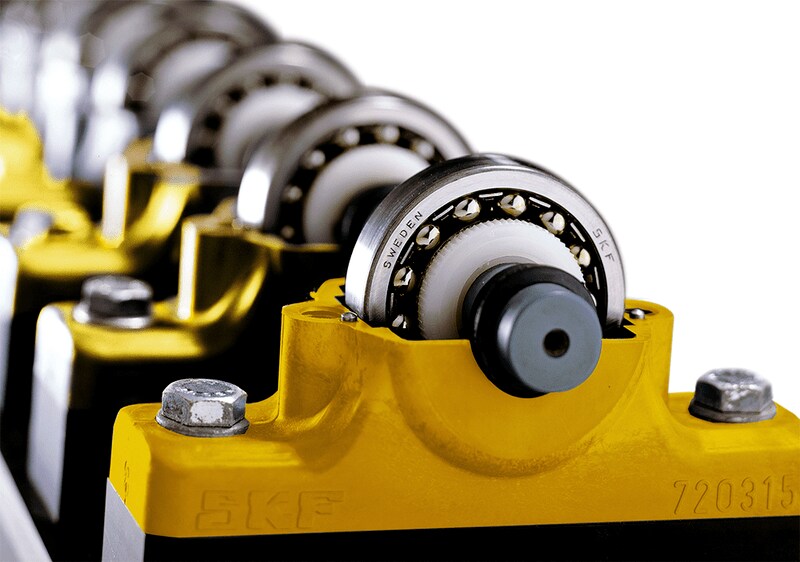
Emcor grease test rig
Corrosive environments demand special properties for rolling bearing greases. During the Emcor test, bearings are lubricated with a mixture of grease and distilled water. At the end of the test, a value between 0 (no corrosion) and 5 (very severe corrosion) is given. Salt water, instead of distilled water or continuous water flow (washout test), can be used to make the test more severe.
Water resistance
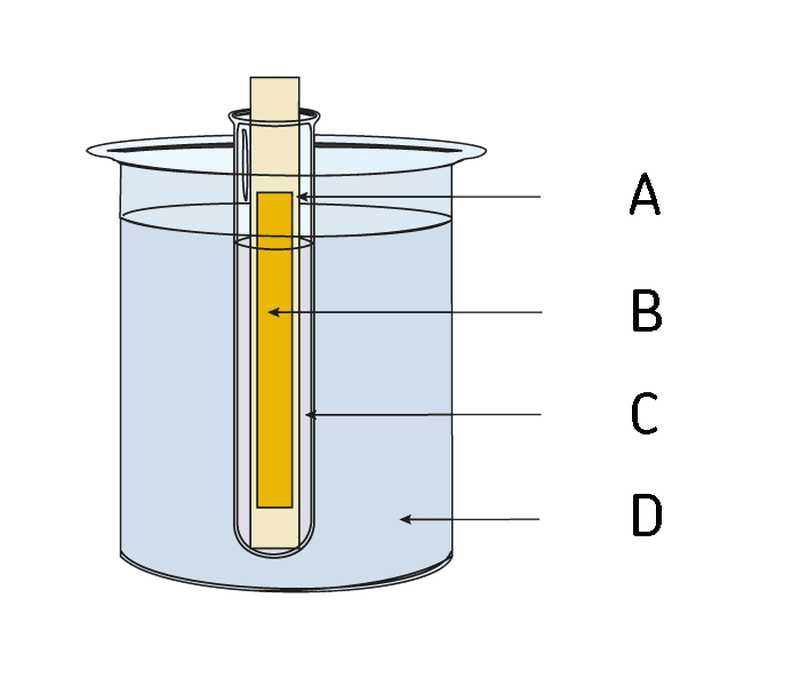
Water resistance test
A glass strip is coated with the candidate grease, which is placed into a water-filled test tube. The test tube is immersed in a water bath for three hours at a specified test temperature. The change in the grease is visually evaluated and reported as a value between 0 (no change) and 3 (major change) along with the test temperature.
A. Glass or metal plate
B. Thin layer of grease on plate
C. Distilled water
D. Temperature controlled bath, e.g. 90 ±1 °C
Oil separation
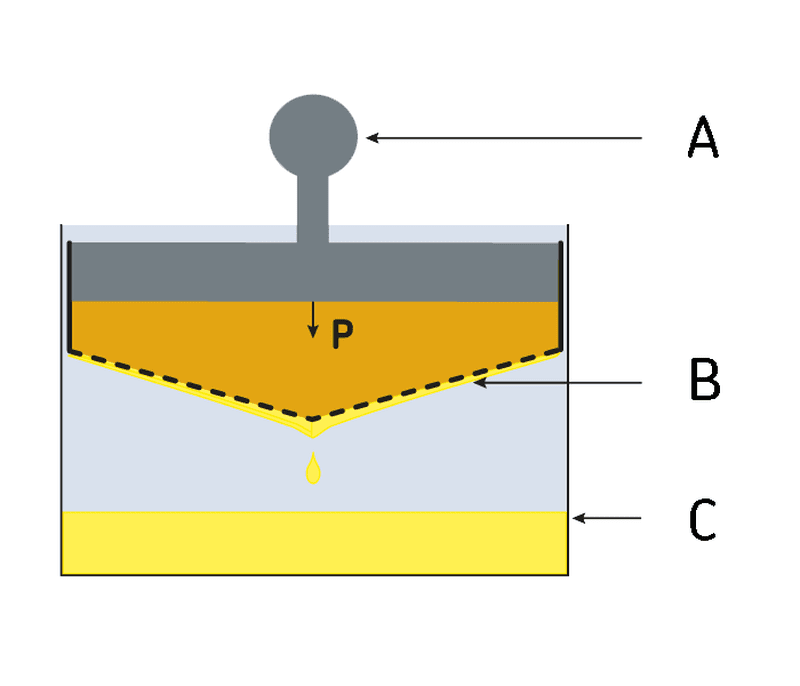
Oil separation test
Lubricating greases release oil when stored for long periods of time or when used in bearings as a function of temperature. The degree of oil separation will depend upon the thickener, base oil and manufacturing method. In the test, a cup is filled with a given quantity of grease (and is weighed before the test) and a 100 gram weight is placed on top of the grease. The complete unit is placed into an oven at 40 °C (105 °F) for one week. At the end of the week, the amount of oil which has leaked through the sieve, is weighed and reported as a percentage of weight loss.
A. Dead weight (gives light pressure on grease sample)
B. Sieve
C. Separated oil
Lubrication ability
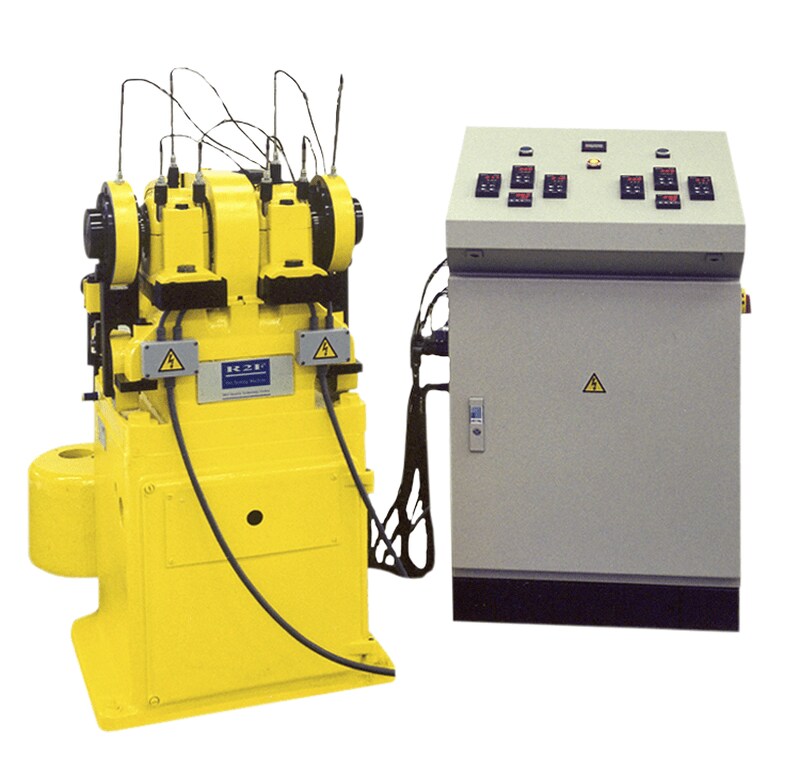
R2F grease test rig
The R2F test assesses the high temperature performance and lubricating ability of a grease. A shaft with two spherical roller bearings in their respective housings is driven by an electric motor. The bearings are run under load, the speed may be varied and heat can be applied. The test method is carried out under two different conditions after which the wear of the rollers and the cage is measured. Test A is conducted at ambient temperature and a “pass” rating means that the grease can be used to lubricate large bearings at normal operating temperatures and also in low vibrating applications. Test B runs at 120 °C (250 °F) and a “pass” rating indicates suitability for large bearings at high temperatures.
Copper corrosion
Lubricating greases should protect copper alloys used in bearings from corrosive attack while in service. To assess these properties, a copper strip is immersed in the grease sample and placed in an oven. The strip is then cleaned and the degradation is observed. The result is rated by a numerical system and a rating above 2 indicates poor protection.
Rolling bearing grease life
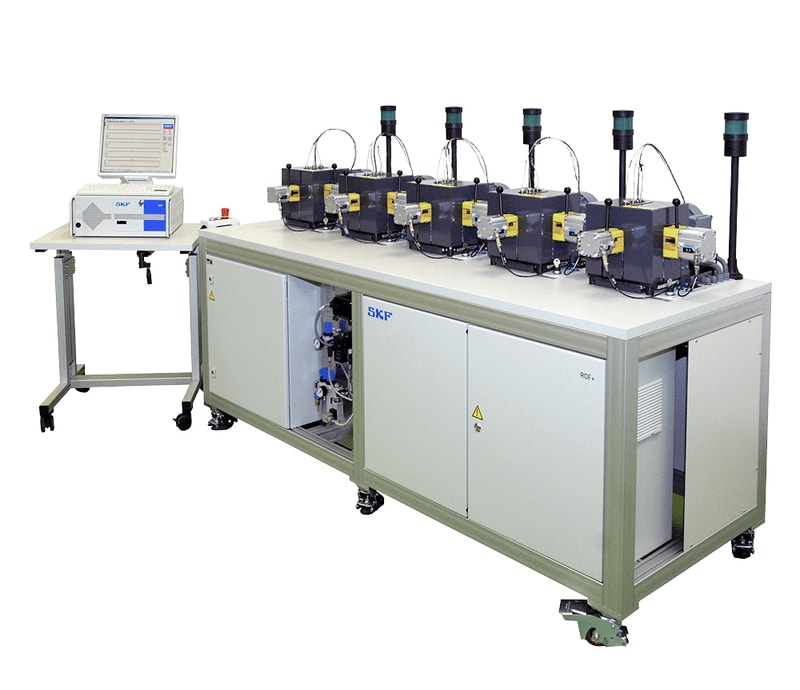
R0F+ grease test rig
The R0F and ROF+ tests determine the grease life and its high temperature performance limit (HTPL). Ten deep groove ball bearings are fitted into five housings and filled with a given quantity of grease. The test is undertaken at a pre-determined speed and temperature. Axial and radial loads are applied and the bearings run to failure. The time to failure is recorded in hours and a Weibull life calculation is made to establish the grease life. This information can then be used to determine re-lubrication intervals in an application.
Extreme pressure (EP) performance
The 4-ball weld load test rig uses three steel balls held in a cup. A fourth ball is rotated against the three balls at a given speed. A starting load is applied and increased at pre-determined intervals until the rotating ball seizes and welds to the stationary balls. Values above 2 600 N are typically expected in EP grease. Under the 4-ball wear scar test, SKF applies 1 400 N (standard test uses 400 N) on the fourth ball during 1 minute. The wear on the three balls is measured and values below 2 mm are considered as appropriate values for EP greases.
Fretting corrosion
Vibrating or oscillating conditions are typical causes for fretting corrosion. Under the FAFNIR test, two thrust ball bearings are loaded and subjected to oscillation. The wear on each bearing is then measured. A wear below 7 mg indicates good fretting protection.